
Once commissioned tanks, pipes and pressure vessels begin to corrode. Periodic inspections identify degraded regions. Engineers need to assess reduced safety margins. This process is known as a Fitness for Service (FFS) Assessment. API-579 defines Fitness for Service Assessment as:
“…quantitative engineering evaluations that are performed to demonstrate the structural integrity of an in-service component that may contain a flaw or damage.”
The ultimate goals of a Fitness for Service assessment is to:
- Ensure the safety of plant personnel while older equipment continues to operate
- Optimize maintenance and operation of existing facilities
- Maximize system up-time
- Enhance long term viability
Governing code bodies have developed guidance for these inspections. Some fitness for service codes include:
- API-579/ASME FFS-1 “Fitness for Service”
- API-653 “Tank Inspection, Repair, Alteration, and Reconstruction”
- B31G ” Manual for Determining the Remaining Strength of Corroded Pipelines”
These codes provide inspectors with empirical methods for addressing flaws and defects. They include methods to determine reduced margin and criteria for repair. Criteria for assessing these defects include:
- Remaining Wall Thickness
- Configuration of Defect Relative To Others
- Location of Defect in Structure
The inspector must assess the integrity of the structure. Issues can arise when interpreting the code. This includes regions where defects are near each other or located in critical regions. In these situations the inspector must analyze a slew of code combinations. The evaluation determines what repairs are required. They need to be cost-effective and code-complaint. Depending on the flaw, repairs can be extensive and require extended maintenance windows to complete. Demonstrating fitness for service of a degraded system is essential to permit continued operation and prepare for extensive repairs or improvements.
Fitness for Service Assessment with Finite Element Analysis
FEA is a refined method to evaluate structural integrity. A FFS assessment using FEA has several benefits over code methods. Advantages include:
Understand the Bigger Picture
Engineers use FEA to evaluate the cumulative effect of closely-spaced defects. Traditional codes fall short in these situations because overly conservative criteria used for generic applications. Often this leads to overly conservative screening criteria and costly repairs. Using FEA, engineers show that even with several defects, structural integrity is acceptable. Refer to our example below.
Dynamic Updates
Using FEA, real-time updates are possible. This allows engineers to incorporate the latest field data and update the assessment. If needed, refinemet is mossible with more data. Engineers can also use FEA to determine the most cost-effective repairs.
Evaluate Critical, Highly Stressed Regions
Code equations do not address all defects. FEA allows engineers to evaluate “critical regions” that transmit large loads. An example of a critical region is the shell to floor transition of above ground storage tanks.
Example Fitness for Service Assessment:
Background
Consider a typical above ground storage tank (AST). The tank design and construction is in accordance with API-650. Recent inspections identified large regions of pitting and thinning. An assessment using API-653 has determined extensive, timely repairs are necessary. FEA is the only method available that can demonstrate the structural integrity of the tank.
Fitness for Service With FEA
The evaluation uses a quarter-symmetric model to save on processing time. The model includes the tank shell and critical joint with the baseplate. The tank model is gridded into a 3″ x 3″ mesh.
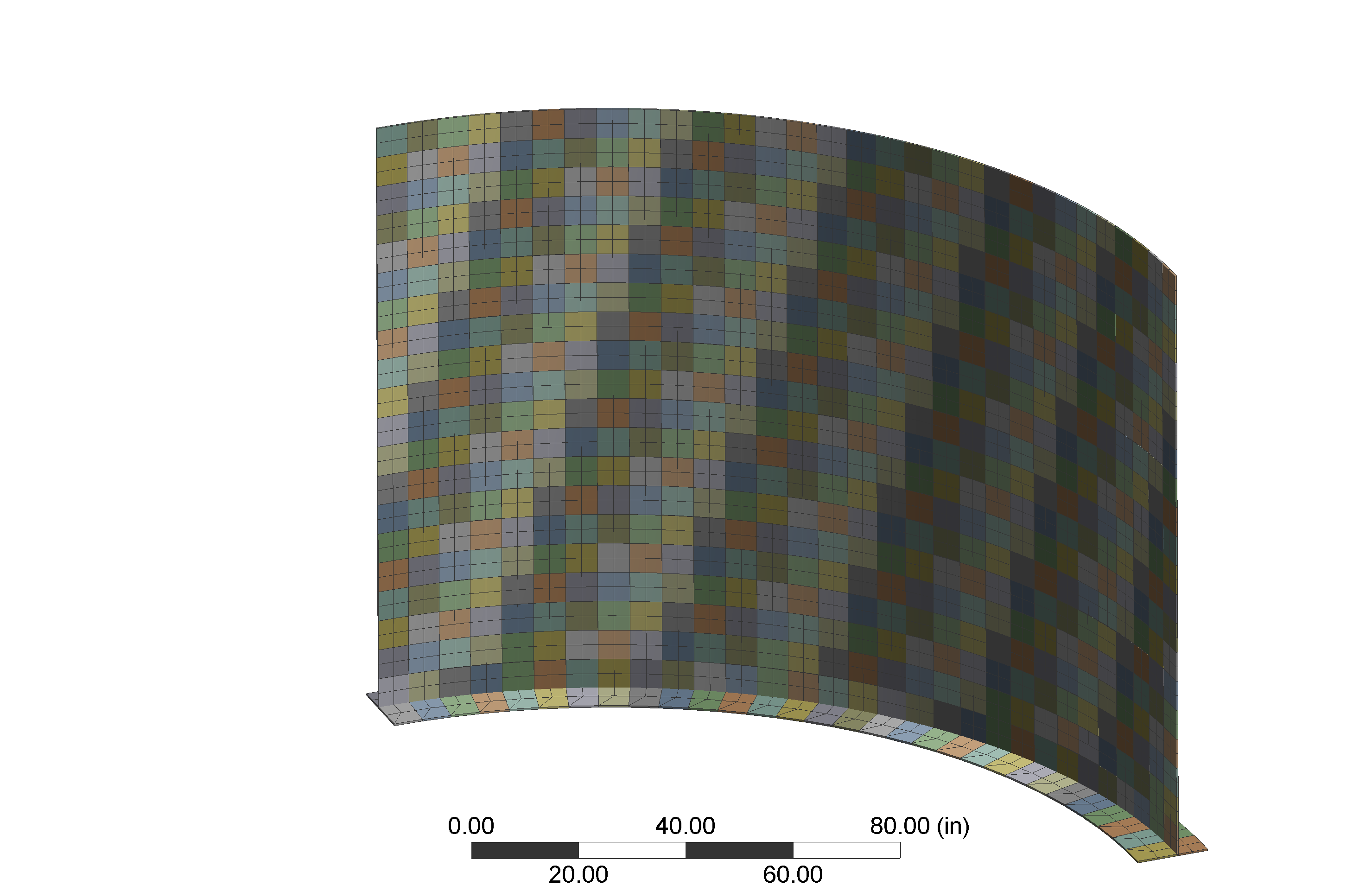
The engineer modifies the thickness of each element based on the minimum field measurement in the grid. This approach conservatively assumes the entire element has thinned. In our example, the tank has a nominal shell thickness of 3/8″ and has thinned to 1/8″ in several regions.
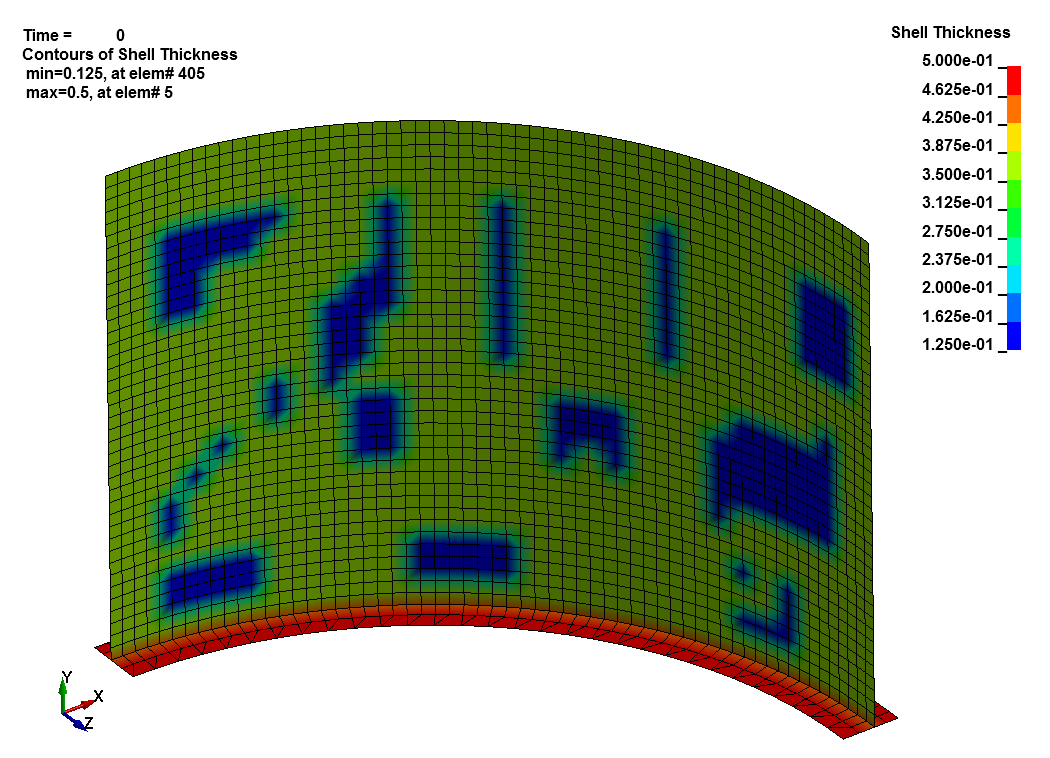
The engineer than applies hydrostatic loading to the tank shell. Pressures are based on the specific gravity of the tank contents.
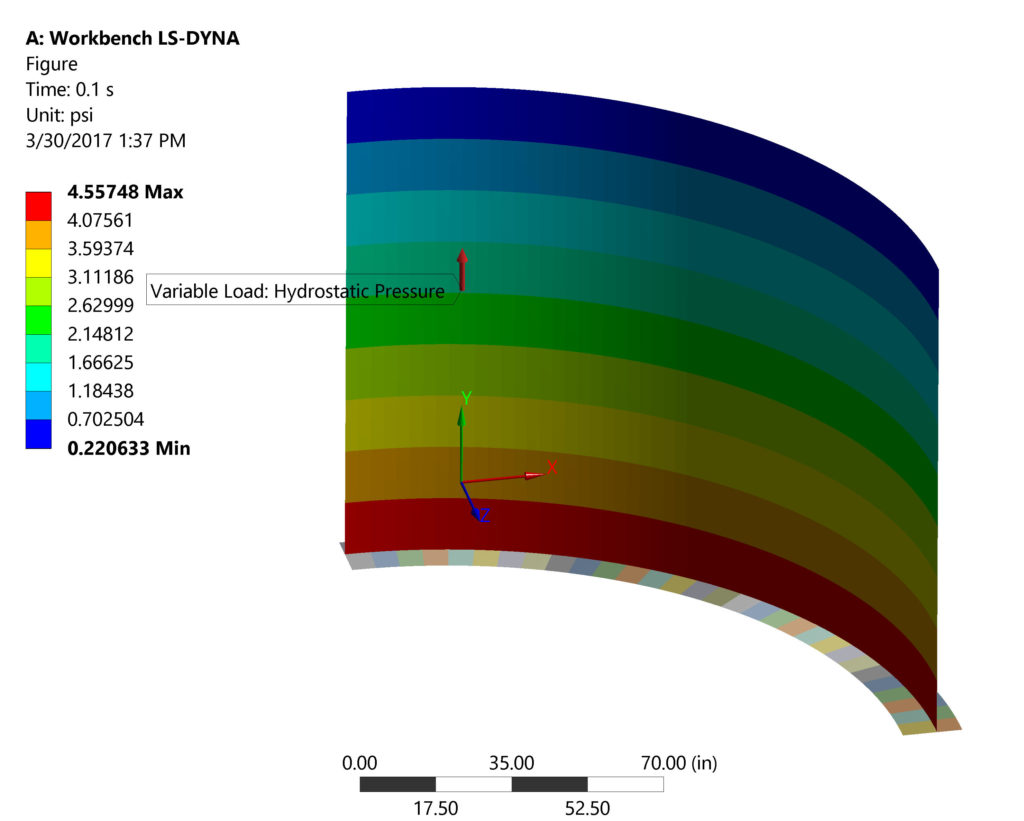
The FEA analysis determines increased stresses in the thinned regions. Stresses are still within code allowable limits. Despite large areas of thinning, the assessment confirms the integrity of the structure. The tank can remain in service with confidence of its structural integrity.

Why XCEED
- Pre-Inspection: Our team of engineers develop minimum wall inspection criteria for inspections. We use FEA to evaluate expected localized thinning.
- Inspection: We support on-site inspections by updating the FEA model during inspection. Continuous updating reduces analysis duration and repair scope. This cuts system downtime.
- Follow-on: We use FEA to scope and size repairs. Our FEA modeling demonstrates code compliance.
- Documentation: We understand Quality Assurance. Our team of engineers prepares reports documenting full compliance with code requirements. Our assessments satisfy regulatory and oversight requirements.
One thought on “Fitness for Service Assessments”
Your is interesting and very educative for anyone who deals with damage in AST.
This gives us more security when using finite elements and a ideal way to treat damage in the shell of API tanks in use.