
Our CFD and FEA Consultants Experience
At XCEED, our FEA consultants have over 20 years of experience using solving some of the toughest problems in the world. We started using FEA in the nuclear industry, pioneering it’s use as a cost savings tool. On one project alone, we saved $8.8M using tools like FEA and CFD.
Our firm is one of the only licensed FEA consulting firms in the country. This means that our FEA consultants are at the top of the pack, and they undergo constant training to make sure their skills are on the cutting edge. We have a wide breadth of project experience from nuclear applications to commercial products. Some examples of our FEA capabilities include:
- Failure Analysis
- Nuclear FEA
- Using FEA in the Design Process
- ASME Pressure Vessel FEA
- Dynamic/transient Analysis
- Blast Analysis
Failure Analysis
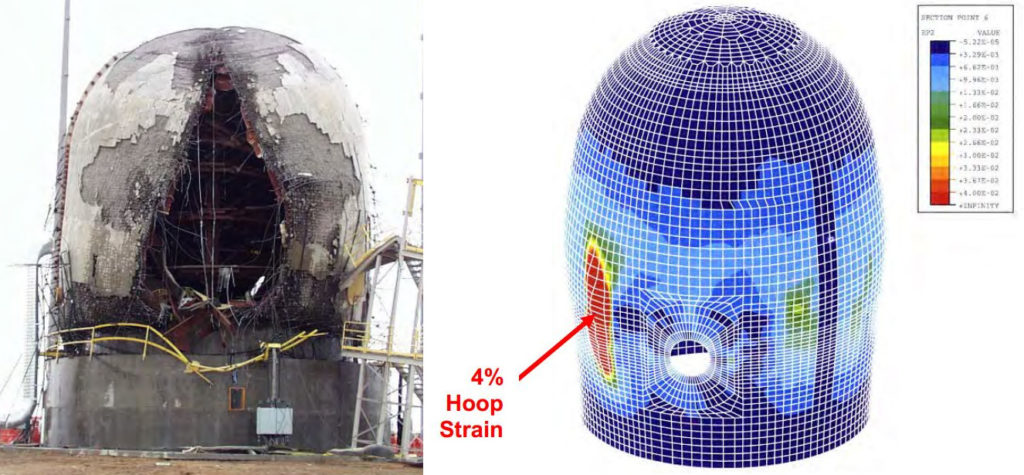
Our team of FEA consultants constantly trains in causal analysis techniques used in many industries from Space Exploration to Nuclear Power. Coupled with our FEA capabilities and experience, we provide a full suite of failure analysis tools. This allows our FEA consultants to quickly and efficiently assist our clients with their failure analysis and root cause efforts.
Our FEA consultants have led many failure investigation teams. Typically, we start by using a tool like the Failure Modes and Effects Analysis (FMEA) or Fault Tree Analysis depending on the failure. We then use FEA as necessary to support or refute claims made during the failure investigation.
Our team of FEA consultants can:
- Evaluate crack propagation
- Preform sensitivity studies
- Simulate failure environment
- Evaluate the effects of wear
Nuclear FEA
XCEED Engineering is one of the only licensed engineering firms that uses an NQA-1 process for FEA. Our team of FEA consultants once worked as designers and systems engineers for nuclear plants, and they’re familiar with both PWR and BWR designs.
Our team of FEA consultants has used FEA as a cost savings tool, reducing the cost of Fukushima FLEX modifications by over $8.8M for one plant alone, and we’ve saved millions for other plants across the country.
We’ve used FEA in the nuclear industry for many applications, including:
- Part 9900 Investigations (Operability Assessments/Determinations)
- ASME BPVC evaluations
- Wall thinning
- Corrosion
- Design Discrepancies
- Support evaluations
We’ve also had the opportunity to work with many plant operators across the country, including:
- Dominion
- Entergy
- Exelon
- Florida Power and Light
- PSEG
- South Texas Project
- Tennessee Valley Authority
All our Finite Element Analyses go through a rigorous review process, and we have a 100% accuracy rate. Many of our calculations have gone through rigorous review by NRC specialists, and our FEA consultants have a 100% success rate with the NRC.
Using FEA in the Design Process
Over 80% of project cost is determined in the design phase of a project. It’s extremely important to optimize the design before fabrication or production.
Our FEA consultants have worked with fabricators, manufacturers and project managers/engineers to help them save cost using FEA. We’ve found that our FEA techniques drive the cost down for the two most important aspects of a project, schedule and scope. Using FEA early in a project has allowed our FEA consultants to save an average of 27% on overall project cost. The average client using our services early in the project saved an estimated $2.2M on their project!
Scope Savings
Limiting project scope is the first step. Our team of FEA consultants has been able to evaluate existing systems, structures and components, showing that they can be either reused or otherwise credited for the project or initiative. An example of this is our tank impact project.
Schedule Savings
By cutting scope, we inherently cut schedule, but it goes beyond that. Our models are parameterized, and saved on our system forever. If your project requires a design iteration, there’s no need to go back through an arduous design process. Our FEA consultants can simply re-run models, and parameterized runs make this incredibly efficient.
Parameterization is an important part of our FEA services. Our FEA consultants can vary certain parts of the model automatically to find the most optimal solution. And because it’s automatic, it makes the design process much faster, cutting cost.
ASME Pressure Vessel FEA

Our team of licensed engineers and FEA consultants have over 20 years of experience with stress analysis for Boiler and Pressure Vessel Applications (ASME Section VIII). The typical process involves using the codes and standards for design; however, unique design problems and degradation issues sometimes make the use of FEA necessary.
An important part of using FEA for ASME Section VIII vessels is contained in article U-2(g) which states:
This Division of Section VIII does not contain rules to cover all details of design and construction. Where complete details are not given, it is intended that the Manufacturer, subject to the acceptance of the Inspector, shall provide details of design and construction which will be as safe as those provided by the rules of this Division.
This allows other methods like FEA to be used in some unique circumstances, but there are still important rules to be applied. ASME has guidance using FEA for Fitness for Service evaluations in API-579-1/ASME FFS-1. Some of the uses for FEA include:
- Corrosion and Pit Evaluations
- Crack Evaluations
- Hydrogen Induced Cracking (HIC and SOHIC)
- Welding Stresses
- Nonlinear Thermal Analysis
Dynamic (Transient) Analysis
Our team of FEA consultants is uniquely qualified for performing non-linear (explicit) Finite Element Analysis. We’ve simulated rapid, transient events like automobile impacts, drop tests, and blast effects for clients across the country.
Our FEA consultants use explicit code for our dynamic, non-linear analyses. This allows us to get faster, and more accurate solutions. We can also vary parameters over time like material properties, temperatures, loads and boundary conditions.
A unique aspect of our transient analysis techniques is our ability to parameterize the analysis. As FEA consultants, we can quickly setup our models for varying conditions or cases, and run through them very quickly, saving our clients time and money on simulation. The larger the project, the more can be saved by parameterization. This is also key for sensitivity studies, and failure analyses.
Our explicit FEA capabilities also extend to 2-way Fluid-Structure Interaction problems (FSI). A great example of 2-way FSI is the model showing the impact of a truck on a water storage tank. The water absorbed 30% of the energy, preventing the tank from puncturing.
Blast Analysis
Our team of FEA consultants have experience with the design and analysis of protective structures and systems. We’ve used FEA to evaluate through air blasts, and the effects on downstream structures. The analyses have also been extended, and used to determine human fragility. Our FEA consultants have also worked with commercial and federal authorities with regards to progressive collapse analyses for large structures.
We’re Here to Help
If you have any questions regarding FEA, please call us at 585-340-7277. Our FEA consultants are ready to help 24 hours a day, 7 days per week. You can also email us at info@xceed-eng.com, or use the contact us form at the side of this page.