Background:
Tornados are one of the toughest natural disasters to design against for Nuclear Power Plants. The come with little or no warning with devastating force. An F5 tornado can have wind speeds of 261-318 mph, faster than NASCAR. They can pick up debris as heavy as a tractor trailer, and toss it with reckless indifference.
Here’s a video from the twisters in Dallas Texas in 2012. Notice the tractor trailers flying through the air.
After the Tsunami at Fukushima, the nuclear industry learned that extreme events do happen, and they need to be ready. The Nuclear Regulatory Commission (NRC) gave orders to sites across the country to bolster protection for natural disasters. Comply with the order, or shutdown.
Site Impact
Many sites were already designed for extreme tornadoes – some up to 360 mph. The NRC added that sites also need to be able to cope with a loss of all AC electrical power, including the failure of diesel generators (which are also protected from tornadoes).
Every site is different with unique challenges based on the new requirements. One site determined that the equipment in the largest building on site needed to be protected from tornadoes. Protecting this building from tornadoes is akin to designing the Chernobyl Sarcophagus.
Alternatives
Protect the Building
Protecting the building was simply not feasible. The cost would have been astronomical, and the design would not have been completed in a reasonable amount of time.
Probability Based
The Nuclear Industry often uses PRA (Probabilistic Risk Assessment) methods to determine the probability of an event like a tornado causing core damage. Using risk didn’t align with the heart of the Fukushima effort, which was to design for extreme events, regardless of the risk.
Local Protection
Not every component in the building needed to be protected. We determined that it was feasible to only protect the critical components.
Design
There was a long run of pipe that was at risk of being impacted by a tornado. This could be easily addressed by plant operators; however, if AC power was lost, then it would be much more difficult to control the plant and mitigate the event.
We evaluated the long run of pipe, and found several areas that were inherently protected by other structures. That left only a few sections of pipe that needed to be evaluated.
The NRC uses Reg. Guide 1.76 as a guideline for plant design against wind driven debris (missiles). For this plant, the bounding strike was from a 15-foot-long, 6-inch diameter steel pipe traveling about 93 mph.
We determined that there was only a few bounding debris strikes. If the piping system survived these strikes, then the piping system would also survive a strike anywhere else. The bounding strikes considered were a crushing strike, and a global deformation strike. The crushing strike assumed all of the energy would go directly into deforming the pipe. The global deformation strike assumed that the strike occurred at a loosely supported section of pipe. With the local strike, creasing of the pipe was a concern, and kinking of the pipe was a concern for the global strike.
Using FEA, we modeled these hits on the piping system, and found that the system would survive both strikes with a minor modification. By adding this small amount of protection, the site was able to save money and time.
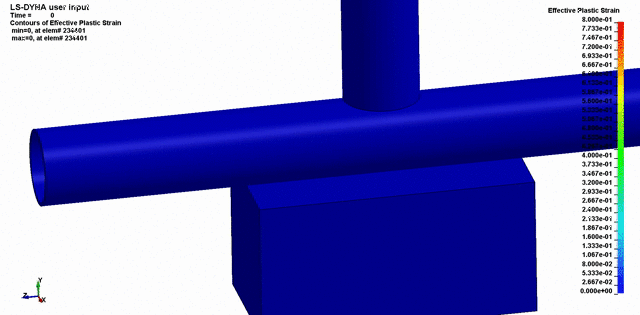