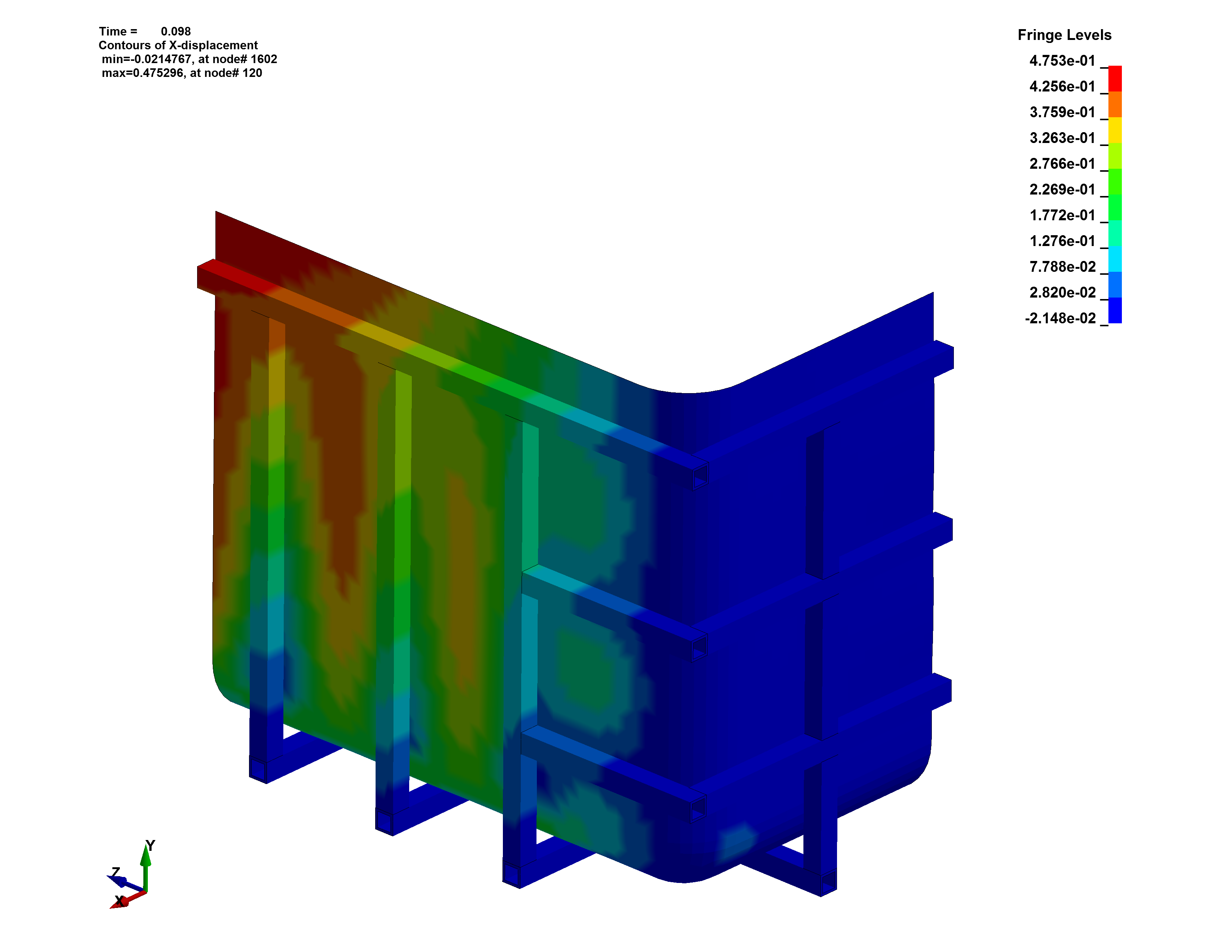
- Discuss benefits of using symmetry in FEA
- Provide a primer in symmetry theory
- Work through a FEA case study using symmetry
Benefits of Symmetry in FEA:
More Cores, More Cores, More Cores….
- Reasonable FEA runtime
- Mesh refinement at areas of interest
- Model comprising entire geometry
The Solution…Symmetry
Symmetry Primer
While some FEA packages are capable of automatically applying symmetric boundary conditions, many are not. An FEA engineer should understand the theory behind the symmetric analysis and be capable of applying the appropriate boundary conditions. Lets review!
Theory
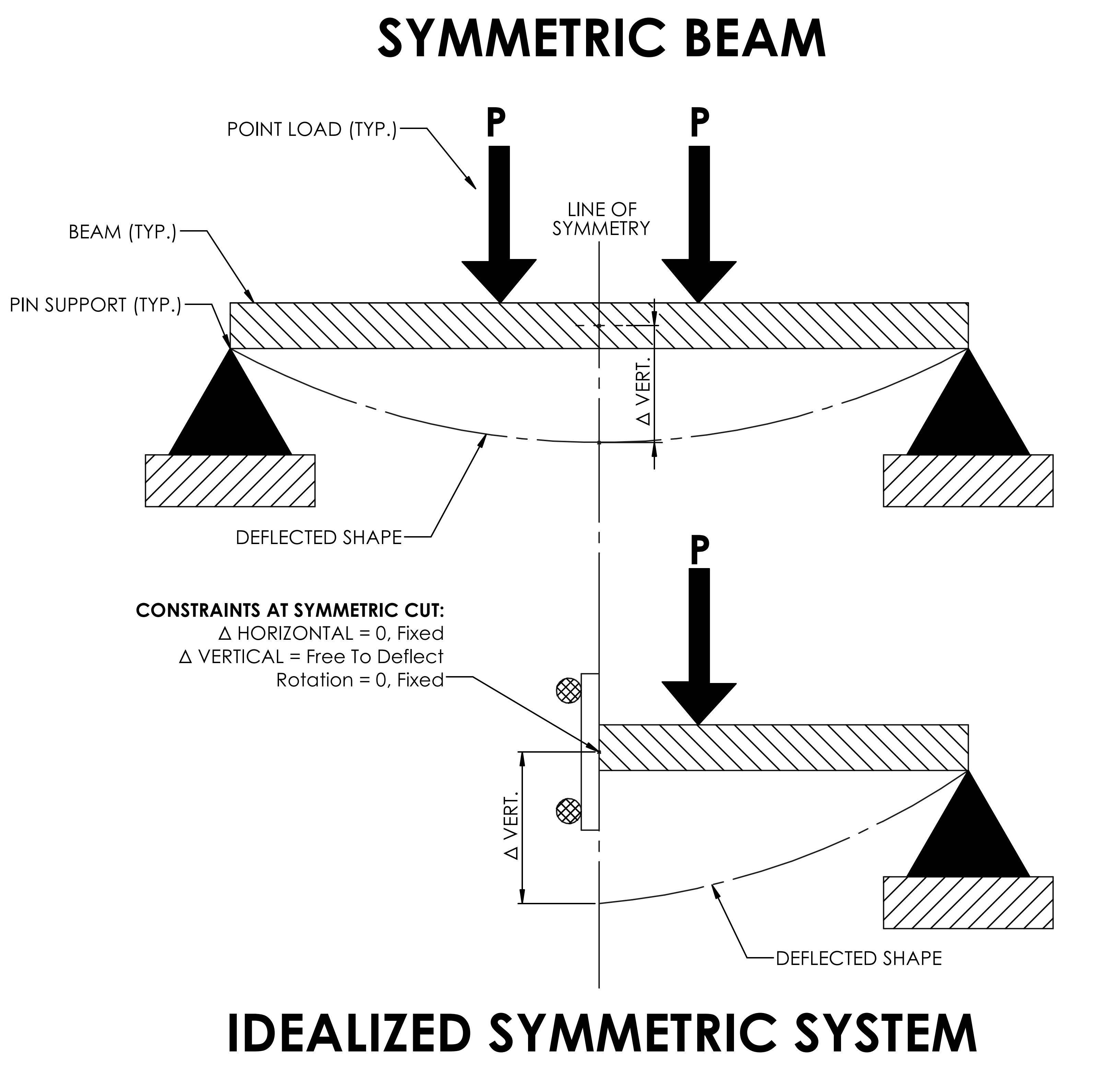
- The rotation at the center of span is zero
- The vertical displacement on both sides of the cut are identical
- The lateral displacement on both sides of the cut is zero
Constraints
- Loads
- Support reactions
- Material parameters
Case Study: FEA Analysis of HDPE Tank
Background
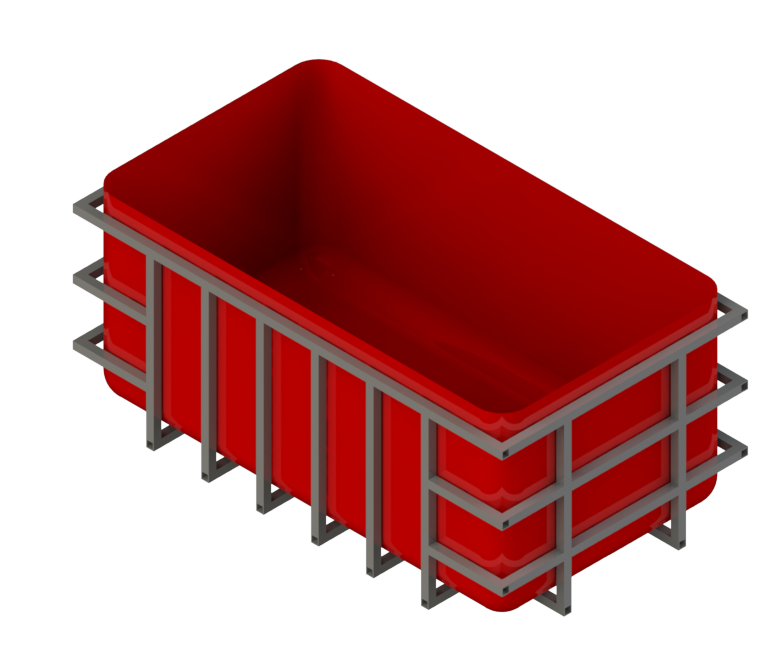
Step 1: Determine Level of Symmetry
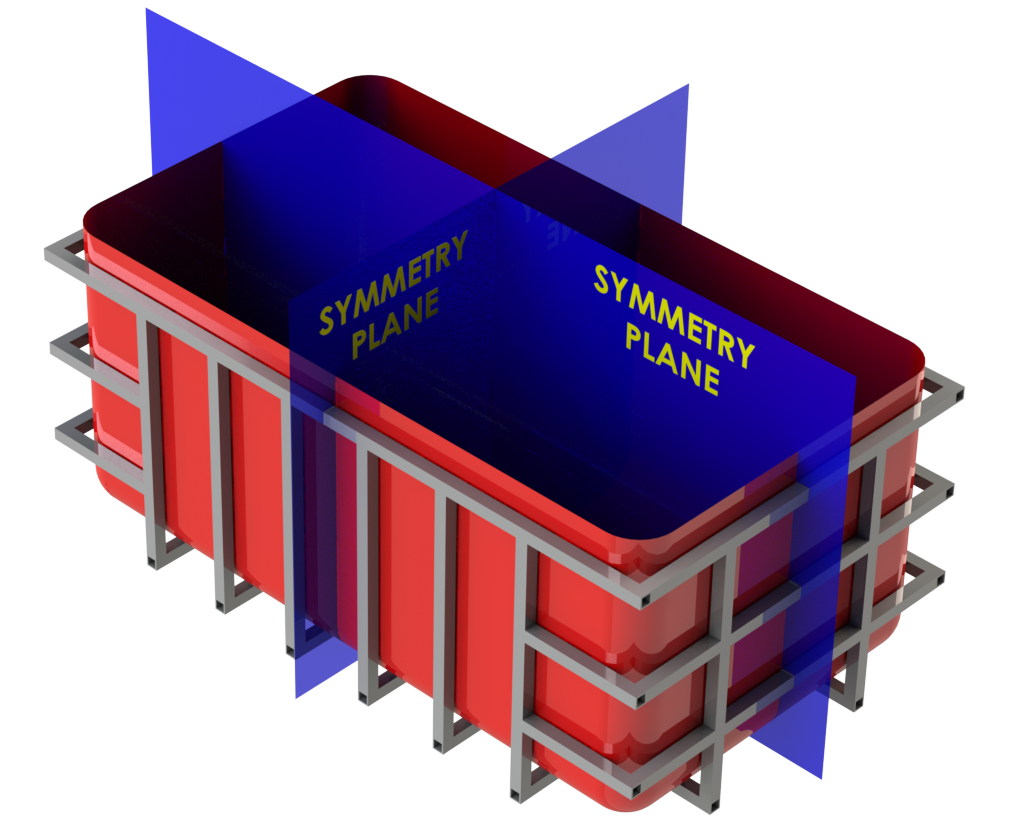
Step 2: Develop Geometry
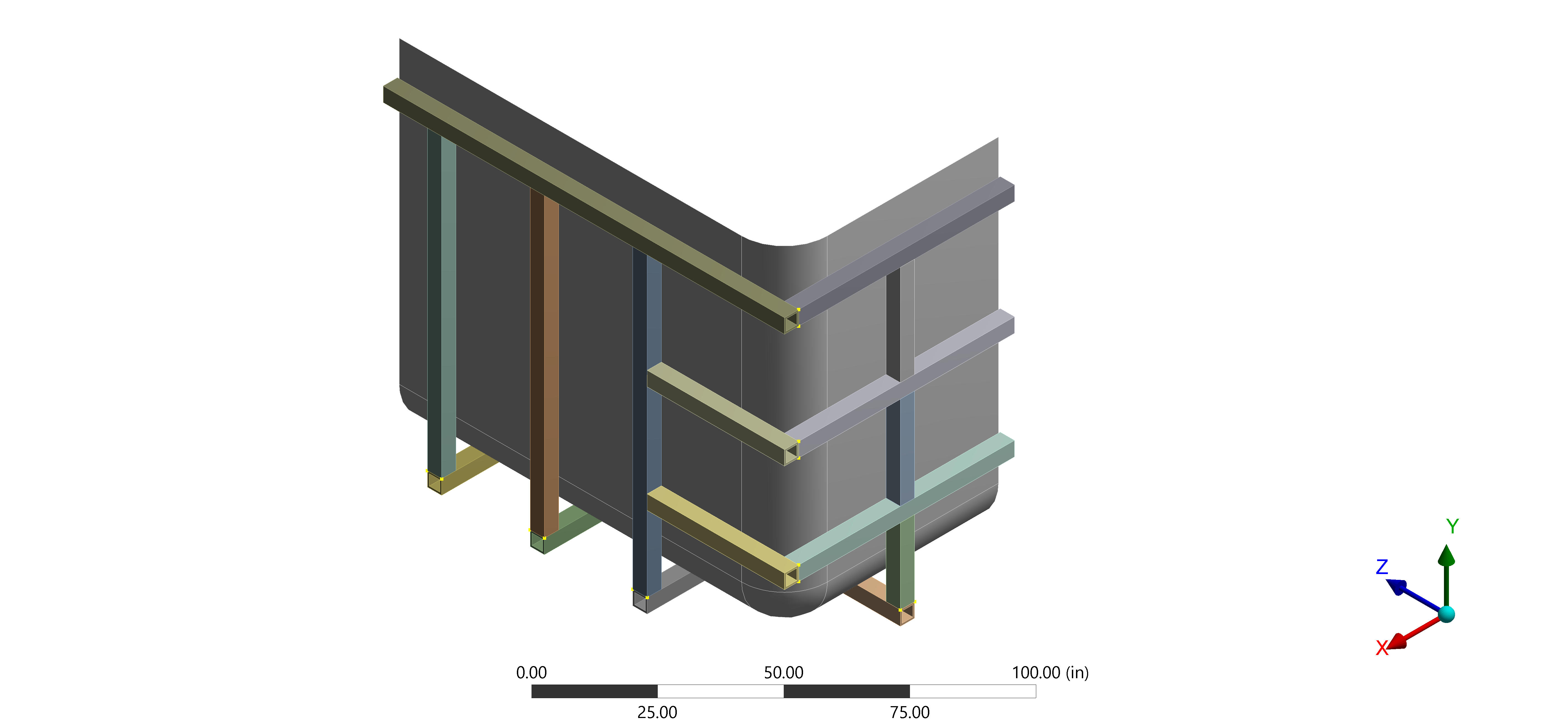
Step 3: Material Properties
Step 4: Mesh
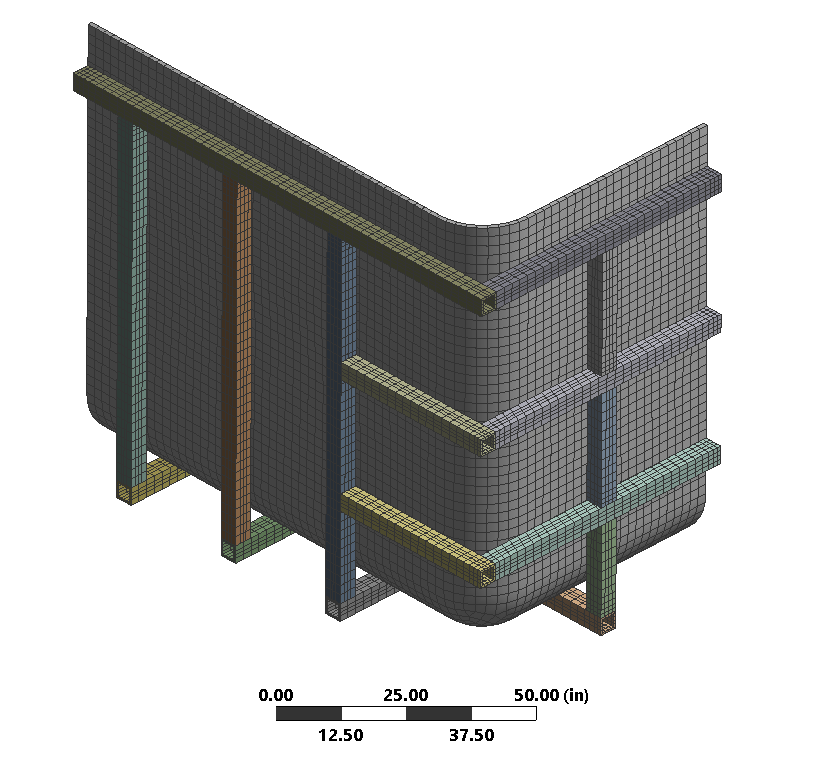
Step 5: Apply Loads
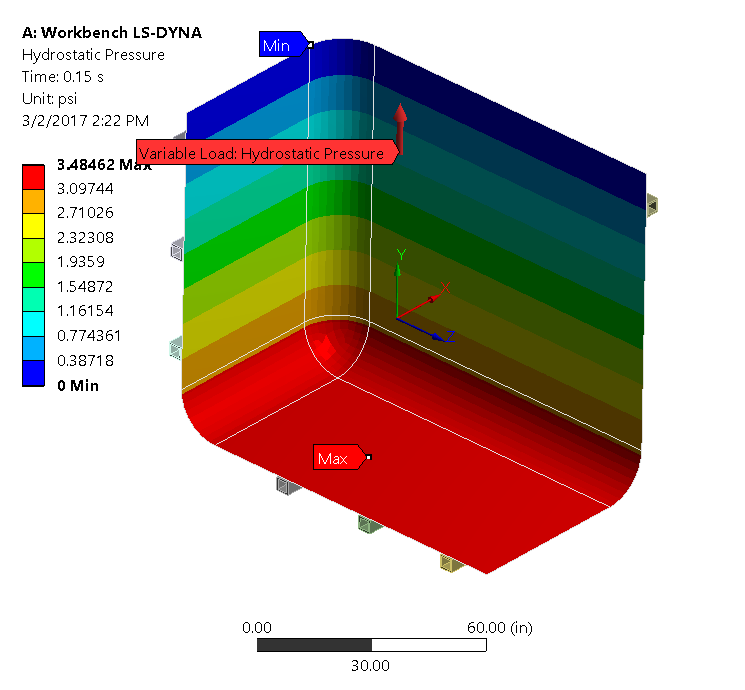
Step 6: Apply Symmetric Boundary Conditions
- Fixed Displacement: Displacement is fixed in directions perpendicular to the plane of cut. This constraint balances the forces in the system. This condition keeps the structure in static equilibrium.
HDPE Tank Lateral Translation Boundary Conditions - Fixed Rotation: Rotation at the cut is fixed at zero. This is because the structural system and loading is symmetric. In any symmetric system (structure and loads) the rotation at the center of the span will always be zero.
HDPE Tank Lateral Rotation Boundary Conditions
Step 7: Apply Remaining Boundary Conditions
Step 8: Set-up & Solve
Step 9: Model Validation
Tank displacement in each direction is shown below:
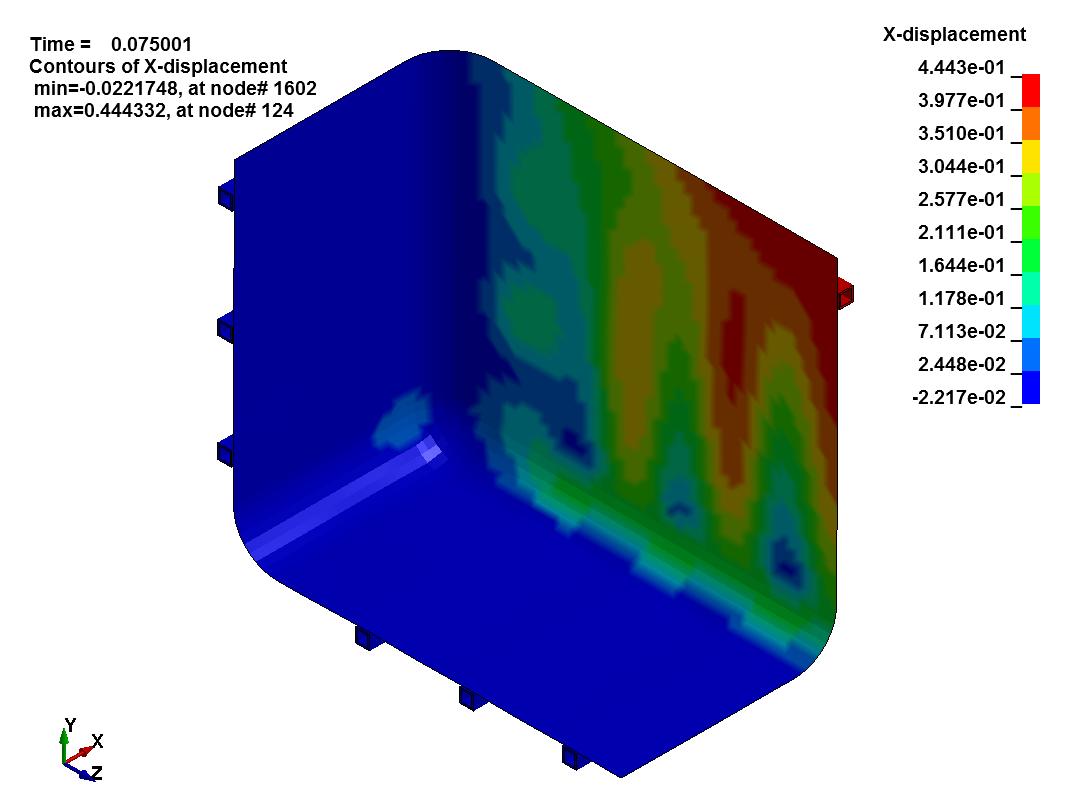
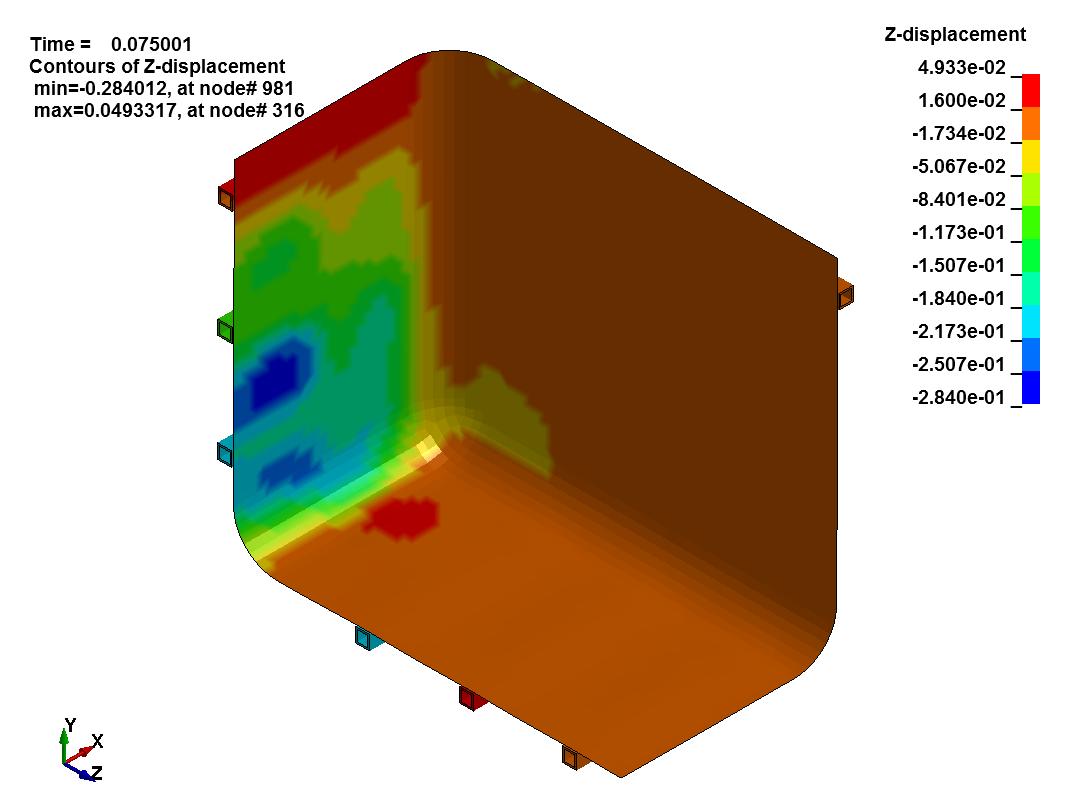
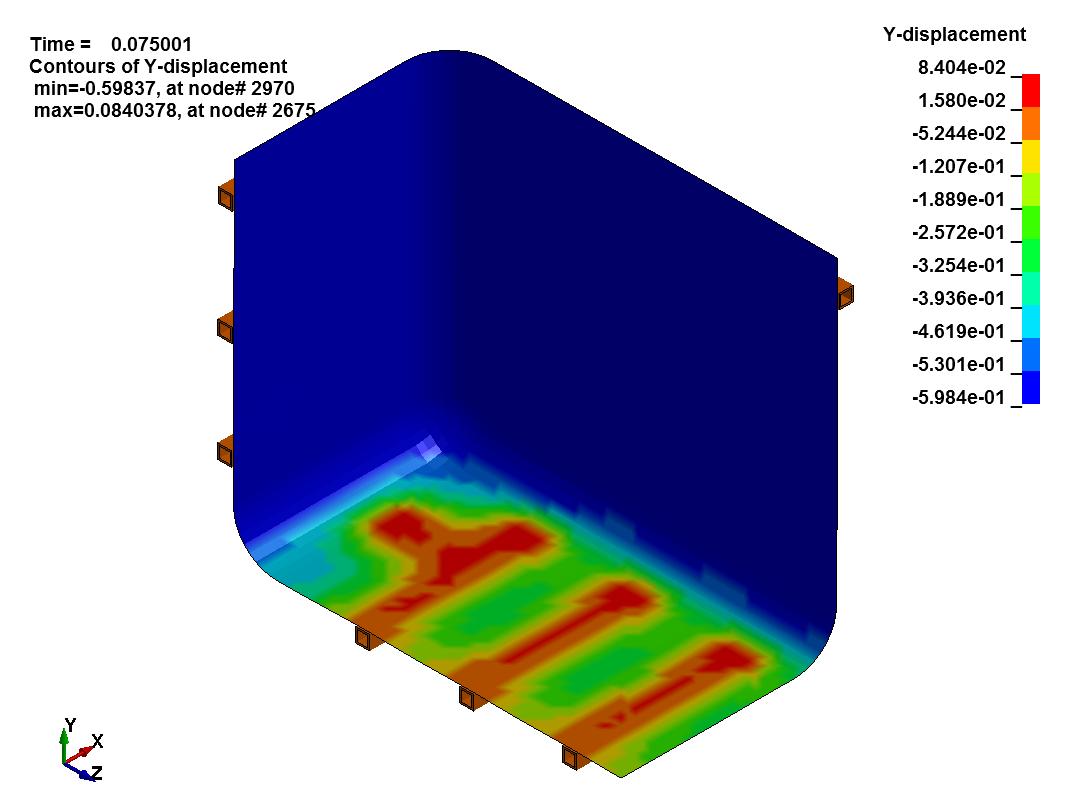
- Translation Parallel To Cut Plane: We see the structural frame and HDPE tank displacing laterally at our cuts. This makes sense, since we expect the tank walls to bow outward under hydrostatic load.
- Translation Perpendicular To Cut Plane: There is no longitudinal displacement of the structural frame and HDPE tank at our cuts. This agrees with the laws of static equilibrium and the tank should remain at rest.
- Rotation at Cut Surfaces: The faces of the structural frame and tank at our cuts do not rotate normal to the plane of symmetry. This makes sense, since we expect the cut to be in the center of a symmetric span where rotation is zero.
Step 10: Understanding Results:
Step 11: Limitations of Analysis
- Non-Symmetric Loading: The model cannot be used to evaluate singular non-symmetric loading.
- Dynamic Analysis: The model in its current form cannot be used for dynamic analysis. This is due to the fact that the model does not contain the mass of the water and lateral loading will result in an anti-symmetric response.