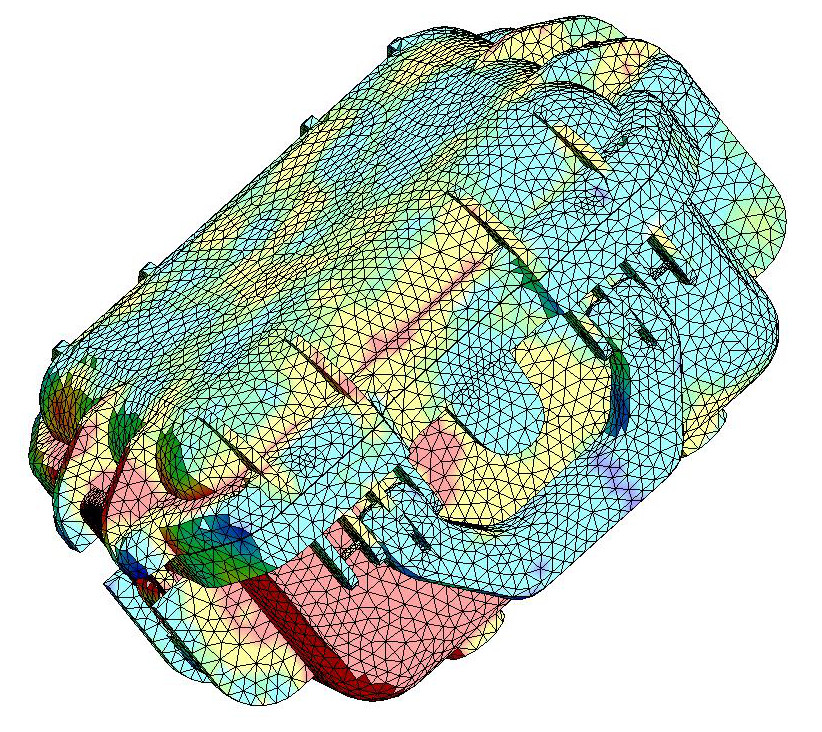
FEA Drop Tests
Today, more and more manufacturers are switching to analytical drop tests before anything goes into production. This helps save time and money, getting your products to market faster, but there’s more than just saving time and money, FEA offers some benefits that drop testing simply can’t do.
1. FEA Lets You See the Full Spectrum
When a drop test is done, you can only see what failed. If you’re lucky, you may be able to see some plastic deformation, but there’s a lot that you can’t see.
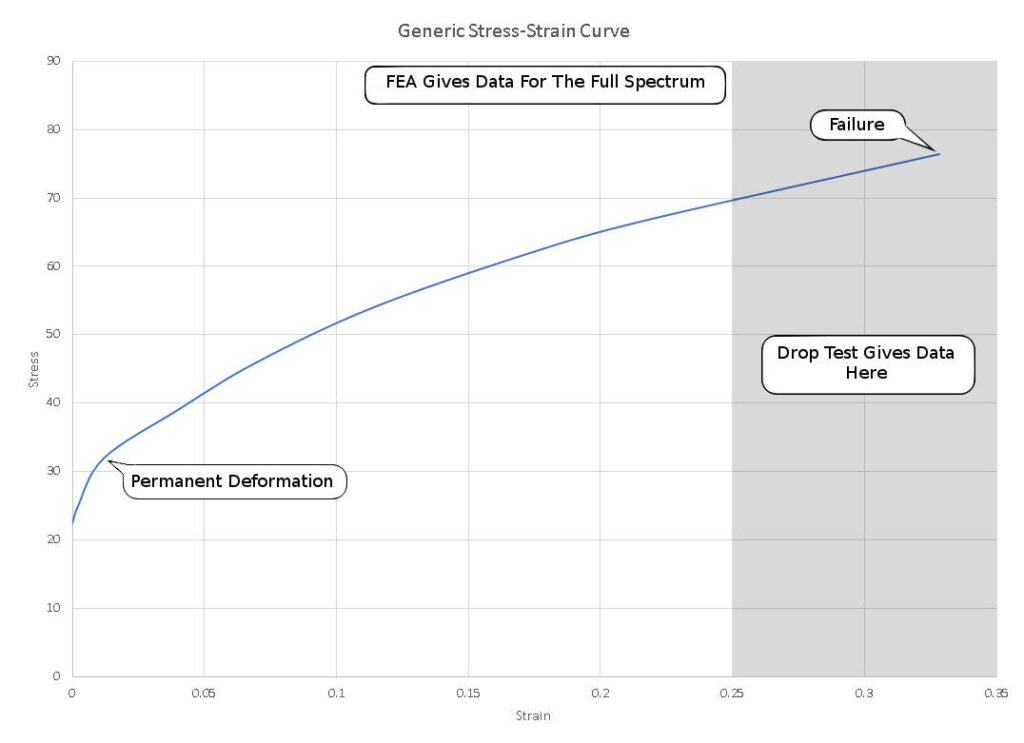
When a material plastically deforms, it can’t ever go back to the same shape it was in before. And each time there’s a large stress, it deforms more and more until it eventually breaks. Drop tests can’t pick this up. With a drop test, you can only see when the material is at or near its limit.
2. More Data, Better Data
Second, FEA gives you data that you couldn’t easily get otherwise. When you do a drop test, you can outfit the product with accelerometers, upload and analyze the data, but there are a few problems with that.
- Everything is subject to instrument calibration
- Acceleration is only able to be measured where to accelerometer is located – good for rigid bodies, but bad if you have a body that can deform.
- One of the biggest problems is that the accelerometer itself can affect your measurements! This is especially true for dropping small items. The mass of the accelerometer increases the mass of the body and throws off the center of gravity. Not good for reliable data.
3. Variation
The third biggest reason to use FEA rather than drop tests is the rapid variation capabilities.
With FEA, the choices are limitless, but here is a list of some of the things that can be varied:
- Impact velocity (drop height)
- Impact Angle
- Material Properties
- Impactor Stiffness (concrete floor, wood floor, etc.)
- Weight properties (e.g. vary case contents)
4. Save Cost with FEA
If drop testing your product is the alternative to FEA, there are likely huge cost savings by switching. Of course, the amount saved depends largely on your product, so let’s look at an example.
If the part is injection molded, you would need to pay for the cost of the mold, which can be tens of thousands of dollars, even for a short run. Then, you need the machinery and labor available to build the prototype, when they could be used for making more product. Then the cost of the drop test itself – engineers, analysts, instrumentation specialists, all spending time and adding to the cost of the drop test.
5. Save Time
Almost every manufacturer has a race to the market with their products. The faster the product can get through R&D, and into production, the sooner the product can be sold.
Developing molds, instrumenting equipment, dropping and analyzing the results takes a lot of time. With FEA, we can take your CAD model of your product, and do an initial drop test within about 1 week! Then we can vary the conditions (see benefit 3), and get real data (see benefits 1 and 2).
Case Study – The Indestructible Case
To show the power of FEA simulation, below is an animation of a drop test for a Pelican case. The short video shows how the stresses are distributed throughout the material.
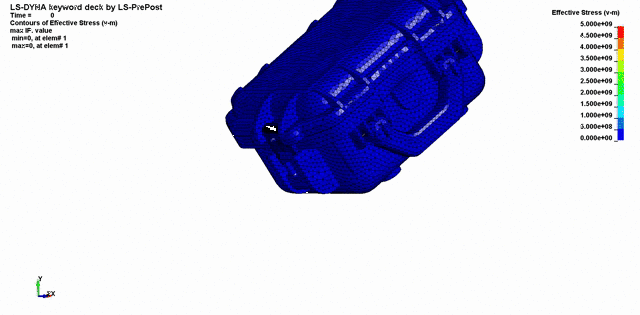
One of the most important aspects of this case is the latching mechanism. Notice that the stresses in the latch are higher. This is because the latch is a cam-lock design, pulling the lid closed.
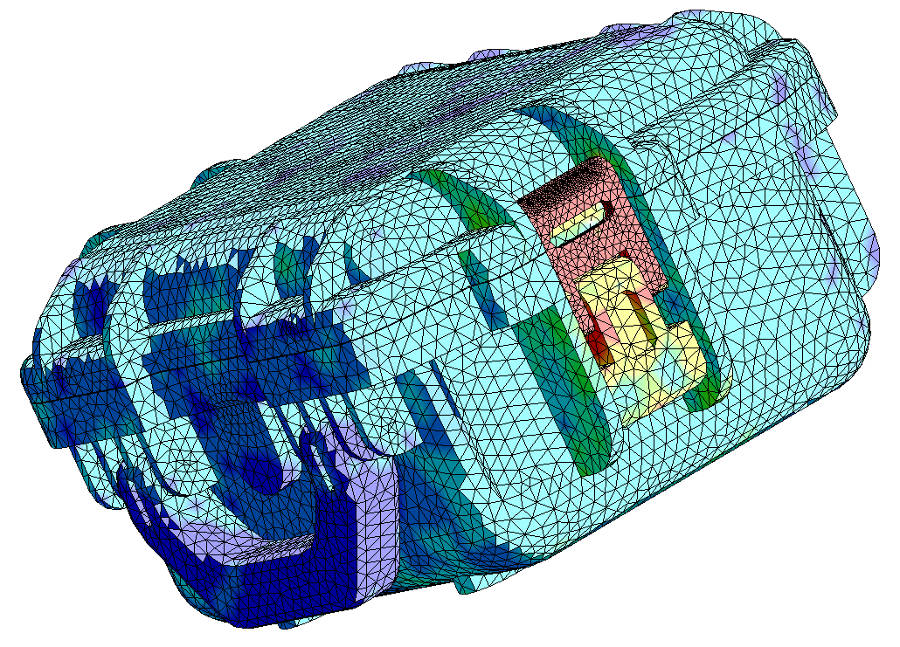
FEA Benefits – Full Spectrum Data
In the stress plot above, you can see the stresses in the material. This is something that drop tests simply can’t do (see benefit 1). We can easily see that the latches are the highest stress component before the drop, and we can even see how stresses are distributed during the drop.
More Data
After performing the full drop test, it’s easy to pull data like acceleration/deceleration, velocities, kinetic energy, peak stresses, and many others. The number of instruments you would need to get this much data would be expensive, time consuming to install and analyze, and they could have an adverse effect on the results.
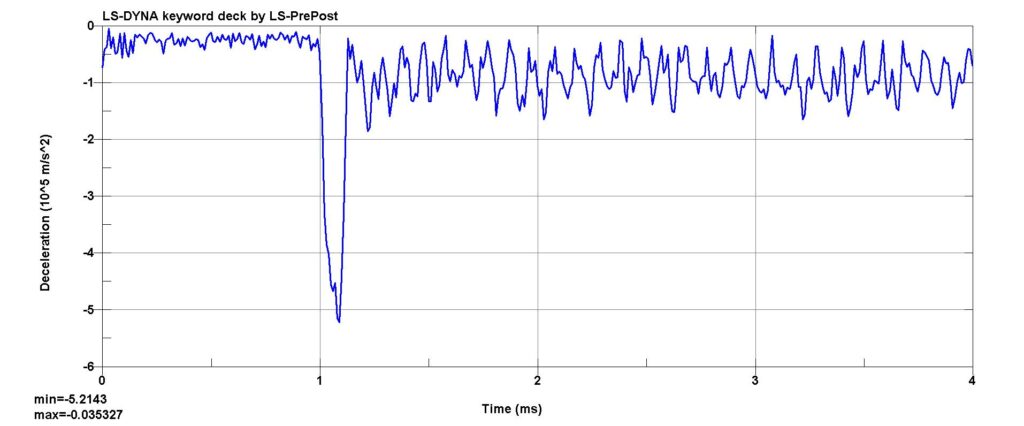
Need More Information?
We would be happy to work with you on your project. If you’d like a free consultation, give us a call, or us the form at the side to leave us a message. We’re always available, and we’d be happy to work with you on your project.